Case Study: Intopack
Discover how Intopack transformed their internal pallet processes with Nipper AGVs and the Nipper Stretchhood. Through a deep partnership, Intopack significantly reduced workload, minimized forklift movements, and created a safer working environment.
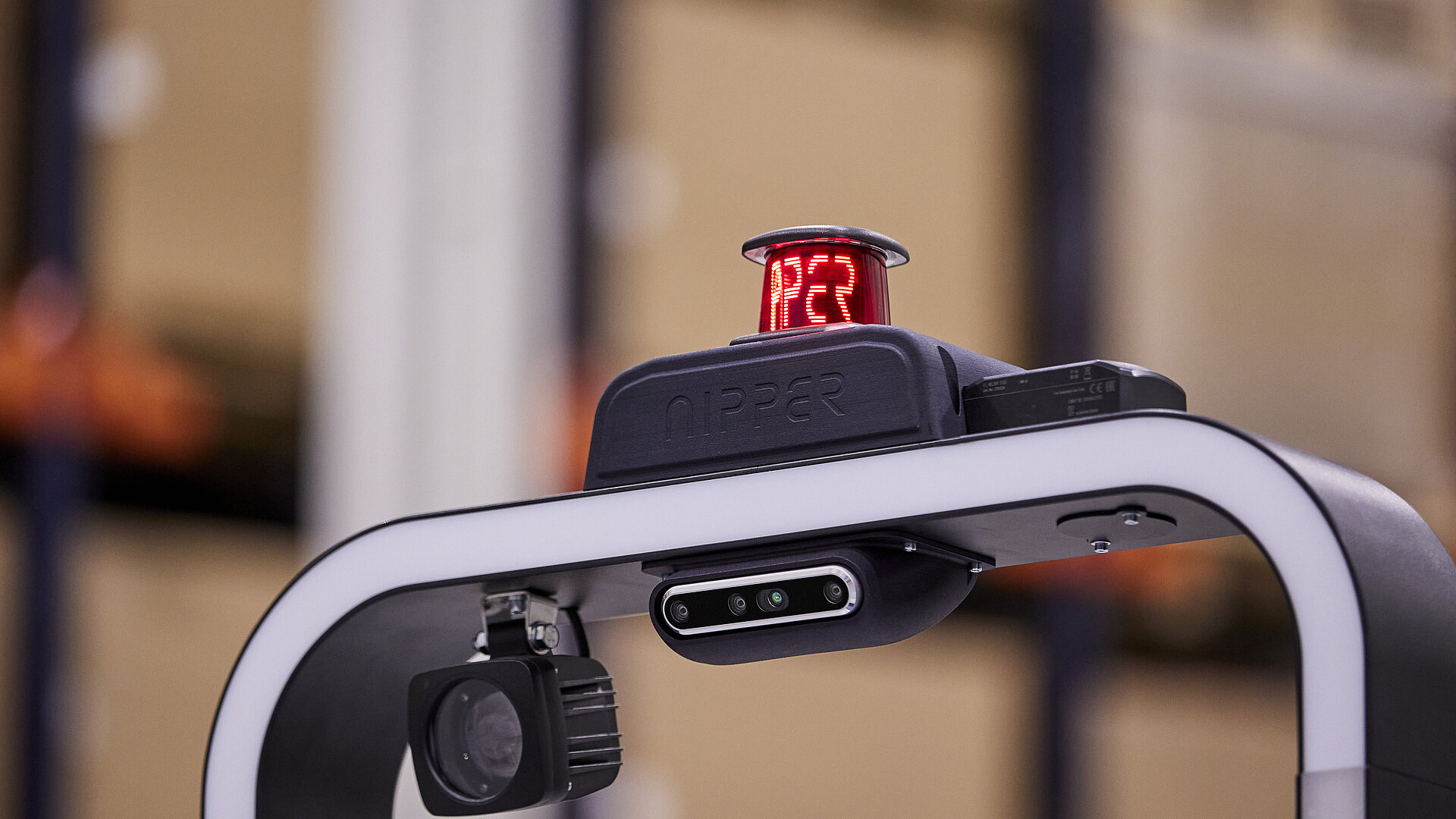
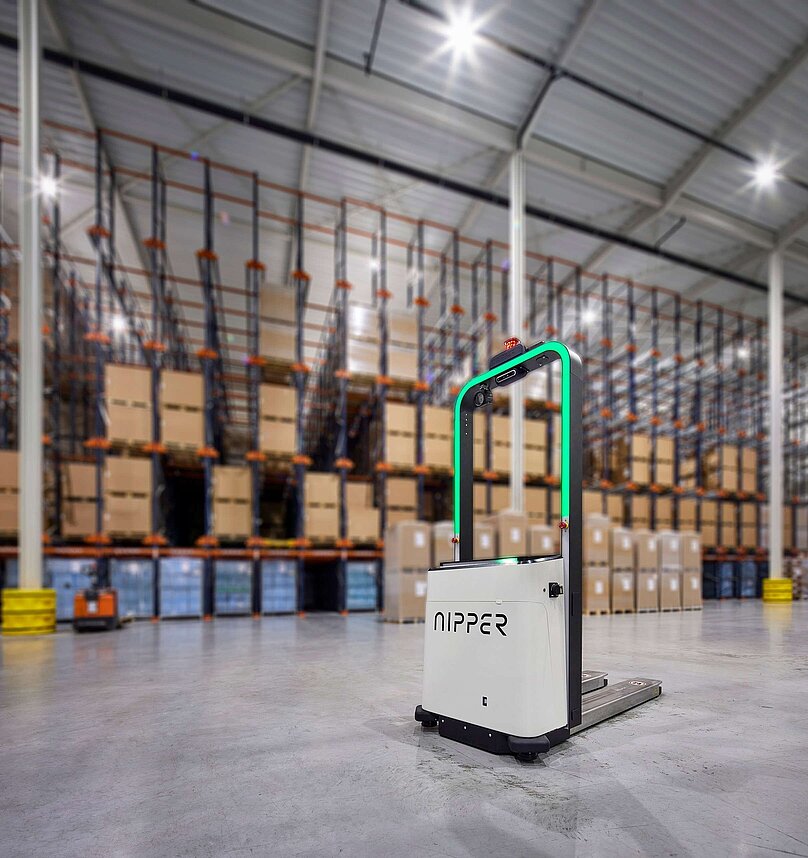
Challenge
Intopack is a plastics processing company that manufactures plastic packaging for the food industry. Within their production teams, Intopack faced a challenge in handling finished products efficiently. Each team, consisting of eight members led by a team leader and two assistants, was responsible for managing the finished product workflow. This process included manually covering each pallet with a top cover, wrapping it, and transporting it to the warehouse. This manual handling was time-consuming and labor-intensive, involving frequent use of forklifts, which also posed safety risks.
The growing demand for automated warehouses in the industry, coupled with the complexity of handling over 2,500 different product types and various pallet sizes and heights, pushed Intopack to seek a new, more efficient packaging and material handling solution.
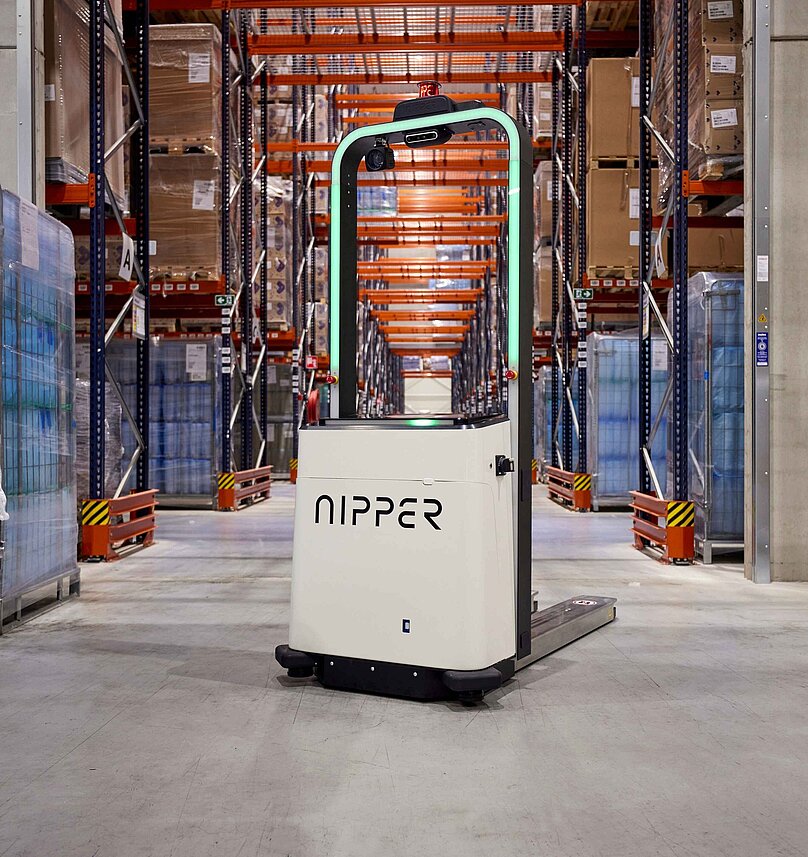
The solution
Intopack partnered with Nipper BV to implement an Automated Guided Vehicle (AGV) system that would take over the tasks of moving finished products within the production environment. The AGV system was designed to streamline the entire process from the production line to the warehouse. Additionally Nipper deployed the Nipper Stretch Hood for packaging the different pallets.
Here’s how the solution works:
- The operator places the finished pallet in the designated pick-up zone.
- The AGV automatically retrieves the pallet and transports it to the stretch hood machine for wrapping.
- A second AGV then takes the wrapped pallet and places it in one of three designated warehouse lanes, based on the type of product.
- Finally, a forklift driver moves the pallet or cage to its final storage location in the warehouse.
In addition to automating pallet movement, Nipper also introduced a stacking solution, allowing operators to stack pallets themselves. This innovation reduced the reliance on forklifts within the production area, significantly improving safety.
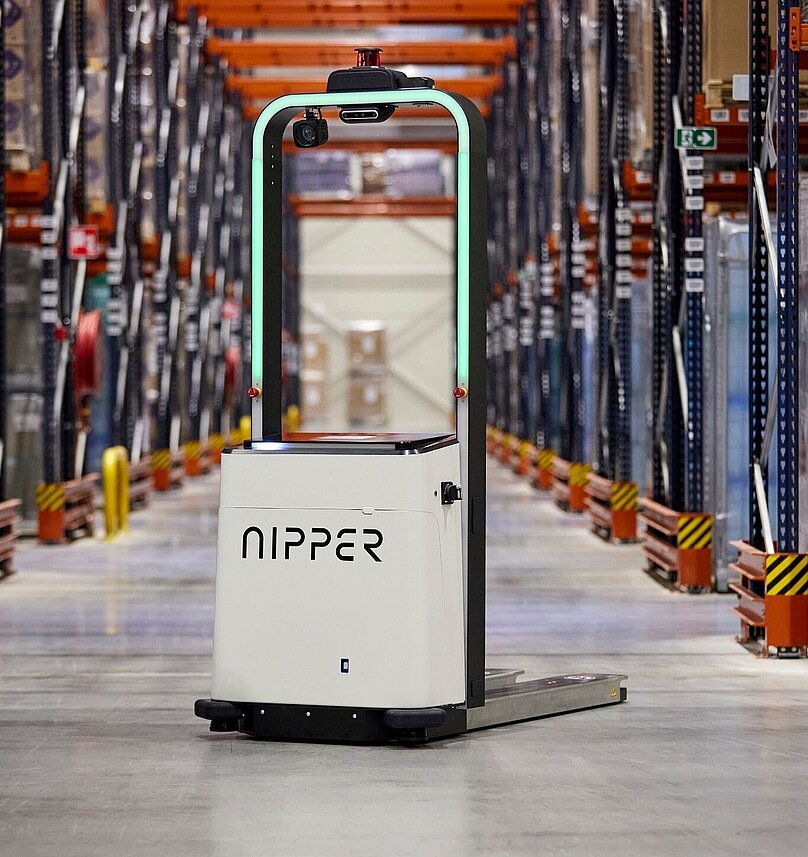
Results
The implementation of Nipper’s AGV system brought several key improvements for Intopack:
- Labor savings: The AGV system took over the manual tasks of transporting and wrapping pallets, freeing up team members for more valuable work.
- Increased safety: By reducing forklift movements in the production area, the company created a safer working environment for its employees.
- Improved efficiency: The automated system streamlined the workflow, reducing bottlenecks and speeding up the transportation of finished products to the warehouse.
- Better packaging handling: The AGV system could manage the complexity of Intopack’s various pallet sizes and product types, ensuring smooth operations despite the diversity of their product range.
- Simplified operations: Nipper provided a total solution, from AGV deployment to stacking, allowing Intopack to rely on one point of contact for all their needs.
- Improved packaging: The Nipper Stretch Hood provides a more efficient and more sustainable way of packing for all different pallet types at Intopack
Find out just how easy the move towards smart can be
From the Nipper Stretch Hood to the intelligent Nipper AGV, all Nipper’s products have been designed as building blocks. They work seamlessly together with our roller conveyor, pallet elevator, turntable, and traverse systems. And can also easily be integrated into existing logistics processes and plants.
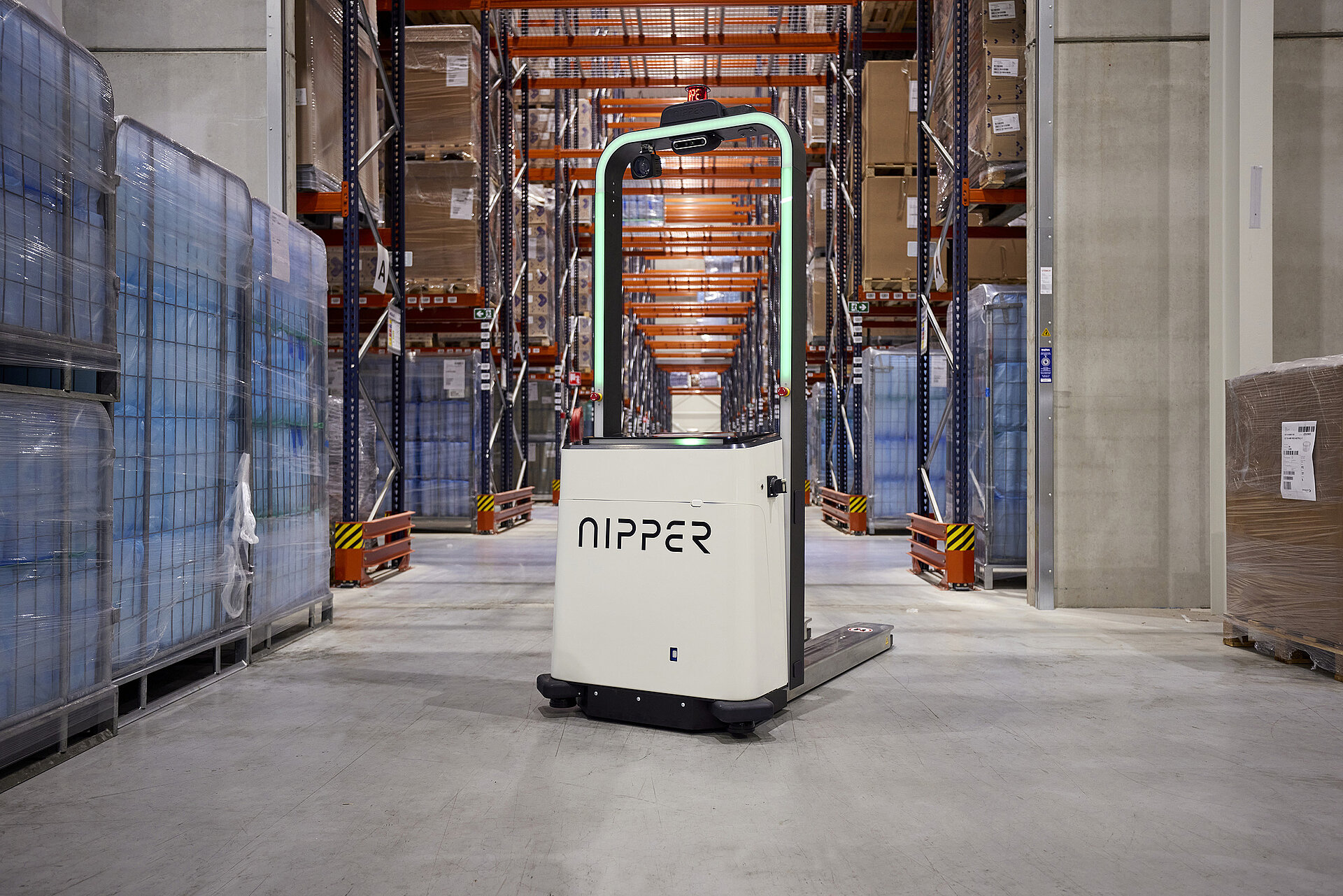